|
Lawn |
|
Lawn is a light-weight, single cloth wash fabric, weighing from 1% ounces to 2% ounces per yard and in widths from 36 inches to 40 inches finished. It is composed of all cotton yarns (bleached) from 1-40s to about 1-100s, and is always woven with a plain weave.
The term "lawn" is derived from "Laon", a city in France which was a large manufacturer of linen lawn.
PLAIN LAWN is made of solid white or bleached yarn in tooth the warp and filling. The fancier grades, or those having a color effect, are produced by printing vines, floral stripes, small flowers etc; in bright colors, in scattered effects upon the face of the goods, the warp and the filling in all cases being bleached yarns. The patterns are always printed, newer woven. Lawn is used principally in the manufacture of ladies' and children's summer dresses, sash curtains, dresses, blouses, nightwear, underwear, lingerie etc. Being a rather sheer fabric, lawn is best adapted to those light running looms in which the action of shedding is easiest upon tine fine yarns used in this style of goods. The warp for this fabric is dressed or beamed upon a regular dressing frame. It is then drawn in on 4 harnesses to permit of freedom in shedding. The plain weave requires but two harnesses, 'but where there are a great number of ends in the warp, the yarn would be very much crowded if tthe warp was drawn in on two harnesses. Therefore, four or more harnesses' are used. Lawn, when finished, should have a very soft, smooth feel. Therefore the finishing process includes 'brushing, very light starching or sizing, then calendering or pressing. 16 square inches equals 6.9 grains. 40x36 equals 1,440x6.9 equals 9,936 divided by 16 equals 621 divided by 437.5 equals 1.419 ounces per yard, 40 inches wide finished.
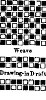
Making Lawn in early 20th century
Carding and Spinning Particulars. The counts of yarns from which lawn is made vary according to the quality of lawn being made. This varies from 40s to 100s. The yarns are made in the third division of mills, as given in a previous lesson or those mills which make high count yarns. In this article we will consider the warp yarn to be 60s and the filling yarn to be 100s. For 'these two counts raw stock of two different lengths of staple and grade of yarn would be used. For 100s a Sea Island cotton of about 1%-inch staple may be used and for 'the warp yarn an Allen cotton of about 1% inches staple. The two cottons would be treated differently at every process' and so we will describe the two cottons at each process. The Allen cotton would be put through the bale breaker, in the manner ascribed in the article of last week, and carried to its proper bin.
|
At this point the GOOD WASTE IS MIXED IN. It is not the general custom to run the Sea Island cotton throug the bale breaker, but to mix it by hand great care should be taken that all the bales mixed are of a uniform length and that the grade of each bale is up to standard. Those bales not up to standard should be shipped back to the broker. The good waste is mixed in at this point, but be sure that the waste boy only puts in Sea Island cotton for, if a shorter staple cotton gets in, it will cause trouble at subsequent machines.
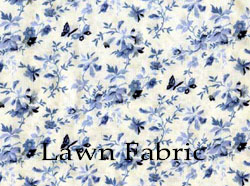
The Allen cotton is put through two processes of picking and an opener. For this class of cotton three processes of picking would be better, for, as it is a very dirty cotton, the extra picking would help to clean it. The speeds of all the picking machines previously given may be used for this cotton. The weight of the lap at the breaker picker should be about 40 pounds or a 16-ounoe lap. The doublings are four into one at the finisher, the total weight being 3.5 pounds or a 12-ounce lap. If an intermediate picker is used, the total weight of the lap should he about 37 pounds or a 12-ounce lap. The SEA ISLAND COTTON is only put through an opener and one process of picking, the reason for this being that the staple is so long that if two processes are used the extra beating that it receives tends to put neps into the staple. The speeds of the opener are slowed down and the speeds of the finisher parts are 'as followsi: The speed of a rigid two-bladed beater should mot exceed 1,000 revolutions per minute. The total weight of the lap should be about 30 pounds or abouiti a ounce lap to the yard. The roving waste should be mixed in at the finisher picker process, as previously explained. The cards should be 'set close for both cottons,, the main difference ibeing tin the setting of the feed roller to the licker-in, which should be set according to the length of staple. The usual points thaiti have been given in previous lessons should be looked out for when, Tunning Allen cotton, the weight of the sliver in front being 65 grains to the yard and the production toeing about 500 pounds for a week of 60 hours, the draift being not less than 100. For Sea Island
ADDITIONAL CARE has to be taken; also certain speeds have to be altered. It has been found that by slowing the speed of the licker-in less neps are put into the cotton and still the cotton is cleaned. In fact, one overseer using this class of cotton lagged his licker-in pulley so as to obtain an extra diameter of 1% inches and found the results excellent, the sliver showing fewer neps than when the usual speed of the licker-in was used. On this cotton it Is the general practlice to use high drafts and sometimes a draft of 165 is used, but for general purposes a draft of about 130 is used. The flats are speeded so as to make one complete revolution every 45 minutes, the extra speed being obtained by lagging the pulley on the cylinder that drives the flats. This, of course, takes out more waste, but it makes less work for the combers to do. The weight of the sliver at the card is about 45 grains per yard. Strip and grind cards the same as stated in previous articles.
|
THE WIRE FILLET. used for cards making sliver for high class yarns is generally firmer than that previously given, and if cards are used for high count yarn the size of the fillet should be as follows: Cylinder No. 34 wire or 110s English count; doffer and top flats, No. 36 wire or 130s English count. The production of a card on Sea Island cotton varies from 325 to 450 pounds per week of 60 hours. Four hundred pounds is a good average. From the cards both cottons are taken- to the comber room and the doublings at the sliver lap are 14 into one. The weight of the Allen lap at the front is 320 grains per yard and the Sea Island weighs 250 grains per yard. The cotton® are then put through the ribbon lap machine, where the Allen is doubled 6 into one, but it is the general custom to double the Sea Island only 5 into one, the weight of lap at the front end being 260 grains per yard for Allen and 200 grains for Sea Island. The laps are taken to the combers, where .they is doubled 6 into one. The speed of the combers should be about 85 to 90 neps per (minute for Allen and 75 to 80 for Sea Island. The amount of waste taken out at the comber 'is important. A good average for Allen is 18 per cent and for Sea Island 20 to 25 per cent. The WEIGHT OF THE SLIVER for Allen is about 42 and for Sea Island about 36 grains per yard. After passing through the comber the sliver is put through two processes of drawing, the weight of the silver at the front being 60 grains per yard for Sea Island and 70 grains for Allen. On all machines when leather top rolls are used for Sea Island, stock should be kept in the best of shape and oiled and varnished frequently. The speed of the front roll on the finisher drawing for Sea Island should be about 320 revolutions per minute or 80 revolutions per minute slower than for Allen. The slobber draws the sliver into .50 hanks roving for Allen, and .80 hanks for Sea Island. The Sea Island is put through three processes of fly frames, the hank roving being as follows: First intermediate, 2.25; second intermediate, 5.00; Jack frame, 18 hank; and for Allen: First intermediate, 1.50; second intermediate, 4.00; jack frame, 12 hank. The twist per inch put into Sea Island, cotton is a little less than the usual amount used for other cottons, the standard for jack frames 'being square root of hank x 1.2. The filling yarn is mule spun and the warp yarn ring spun, the following particulars being used: Gauge of frame, 2% inches; diameter of ring, 1% Inches; length of traverse, « inches; speed of spindle, 10,000 revolutions per minute; twist per inch, 34.86. The warp yarn is then taken to the spoolers and from here to the wrappers, where it is run on beams and taken to the slashed. The following is a good size to use: 100 gal. Water, 54 pounds potato starch, 2 pounds Yorkshire gum, 1% pounds soap.
|
Finishing Particulars. Lawns have to be very carefully handled in the (bleaching process. They are starched1 with an ordinary starch mangle with from 8 to 12 ounces best white German dextrine pea- gallon, mixed cold, and hailed tor one hour, with a little blueing added to shade required. They are then finished on the stent-er machine, dryed with hot air, care being taken to keep the pieces perfectly straight. Some ibleachers handle each piece separately from start of process to finish, bleaching, starching by .hand tin a tub anid 'drying in a frame in the stenter stove. By so doing the ipieces do not gelt drawn and the filling is always straight across the piece. Lawns are often tinted light shades of blue, pink, cream, eoru, pearl, green and other light tints with direct colors added to the staroh, the direct colors being used generally. The basic and acid colors 'are also tinted to make bright colors |
|