Velveteens, also termed fustians and velverets are cotton cloth made in imitation of velvet. They are heavy cotton fabrics in which the distinguishing effect is formed by the points of the fibres in the filling yarns, termed the pile, being presented to the vision, and not the sides of the yarns as in the majority of fabrics. They are principally used for dress and hat trimmings, suitings, and upholstery, having exceptional wearing qualities and showing a full, deep color. Corduroys are sometimes termed velveteens, the same principle of construction being adopted in both fabrics, but a corduroy is distinguished . by having a corded stripe effect running lengthways of the piece, the dividing line between each stripe showing both warp and filling. In the simplest type of velveteens the pile filling, after being cut, hides the warp entirely from the face. To accomplish this the goods are made with a comparatively small number of ends and large number of picks per inch.
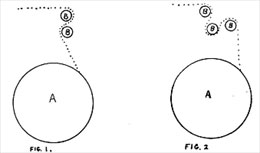
A fairly heavy loom is necessary. Figures 1 and 2 illustrate two methods of arranging the whip rolls and yarn when weaving some of the heavier picked goods. In each figure A represents the warp beam and B the whip rolls. The dotted line indicates the direction of the yarn.
The goods are usually woven two or more widths in the loom, with split selvedges. In order that the fabric may remain firm after the pile picks are cut, ground or binder picks are inserted regularly, working either plain or twill as may be desired. The filling for these picks is similar to that used for the pile, only one shuttle being used.
PURPOSES. For dress and trimming purposes velveteens are usually of a solid color, being piece dyed. For upholstery purposes the goods are dyed, printed, embossed or stamped. Panel and stripe patterns are also made by cutting a raised figure on an uncut ground, or vice versa, by painting or by the pyrogravure process, burning. When STAMPING velveteens the goods are passed between two cylinders. The upper cylinder is of iron and is heated from the inside. The pattern is engraved or sunk into this. The lower cylinder is of hard wood. The pile is compressed by the projecting part of the upper cylinder, causing the pattern to stand out in relief from a dull ground, of vice versa.
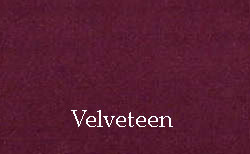
|
PAINTING ON VELVETEENS is essentially a hand process. The colors have to be free from oil that they may not spread beyond the limits intended. In the pyrogravure process of making patterns on velveteens, the sketch is first made and placed in a pantograph machine. With a platinum stylus heated to redness the operator then burns out the pile along the lines traced, leaving a very clear pattern. From the time a velveteen leaves the loom to the time it is ready for cutting, it has to be passed through several processes. It is first put through a BACK STARCHING AND DRYING MACHINE. After drying, the better grades are raised on the under side to make a softer feeling cloth. The lower qualities are not raised on account of the tendency for the process to weaken the cloth. The goods are then, while under tension, saturated with a weak milk of lime, the solution being brushed into them on the face side. The next process is drying. This is done by a device in which rods are automatically inserted below the fabric, so that the latter hangs down in loops. After drying, the cloth is folded and passed to the brushing machine. This machine removes the lime and loosens the filling floats so that the knife can readily enter beneath them. The cutting process proper now takes place, being done either by machinery or by hand. Carding and Spinning Particulars. The fabric for which the carding and spinning particulars are given below is made up in several grades. For this article only two grades will be considered, a coarse one having a warp of l-28s and l-40s filling; and a fine grade, the warp yarn of which is 2-70s and with a filling of 2-60s yarn. This fabric, all grades, would be made either in the second or third division of mills as given in a previous lesson. We will consider THE COARSER GRADE first. This would be made from a me dium grade 1 5-lfj inch staple cotton and run through the bale breaker with blower and endless lattice connections, so that it will reach the mixing bins in a dry, open state. When feeding the bale breaker do not feed one entire lap before starting on another.but open several laps around the bale breaker and feed from each bale alternately. The mixing should be • AS LARGE AS POSSIBLE. so that there will be less variation in the yarn than when small mixings are used. The good waste from the machines up to the slubber is mixed into the bin as it is collected. The cotton is next put through an opener and either 2 or 3 processes of pickers. It is the general custom nowadays to use 2 processes, but the particulars for three processes will be given. If one process is left out, use particulars given for breaker and finisher pickers. Feed the Eopper of the opener so that it is always more than half full, because the more cotton there is in the hopper the more cotton will be taken up by the spiked apron and thus a more even sheet will be presented to the beater, which is generally of a porcupine type and is speeded up to 1,000 revolutions per minute. The speed of the beater at the breaker picker is 1,500 revolutions per minute. The total wedght of laps at the front of this machine is 40 pounds or a 16-ounce lap. These laps are DOUBLED FOUR INTO ONE at the intermediate. At this machine the speed of the beater is 1,450 revolutions per minute. The total weight of the lap at the front is 37 pounds or a 10-ounoe lap. These laps are doubled four into one at the finisher picker, the total weight of a lap at the front being 39 pounds or 14% ounce lap. The speed of this beater is 1,450 revolutions per minute, which gives the cotton passing through it 42 blows or beats per inch. Each lap, as it is taken from the front of the finisher picker, should be weighed and all those laps ranging over a half a pound from the standard, either way (light or heavy), should be run over again. The CUT ROVING WASTE is mixed in at the back of the finisher picker in proportion of one lap of roving waste to three laps of raw stock. The cut roving waste has to go through a special process to take out twist and from here it is put through a picker which forms it into a lap, then it is mixed with the raw stock as above. From the picker the laps are-taken to the card. The draft of this machine should be about 110. The settings should be medium and the wire fillet used would be No. 35 for doffer and flats and No. 34 for cylinder. The speed of the top flats should be one complete revolution every 40 minutes. The sliver at the front should weigh 65 grains per yard and the production for a week of 60 hours should be about 800 pounds. The sliver is then put through THREE PROCESSES OF DRAWING, the doublings at each process being six into one. The speed of the front roll is 400 revolutions per minute at each process. The sliver should weigh about 70 grains per yard. This is then put through the slubber and made into .50 hank roving. The roving to be used for 28s yarn is put through two processes of fly frames, the hank roving at the first intermediate being 2 and at the second being G. This is then taken to the ring spinning room and made into 28s yarn on a warp frame having the following particulars: Gauge of frame, 2% inches; diameter of ring, 1% inches; length of traverse, 6% inches; speed of spindles, 9,700 revolutions per minute. From here it is passed through the spooler .which takes the yarn from the cop and winds it onto a spool. From here it is wound onto a beam and several of these beams are put up at the ends and run through the slasher and wound on to a beam at the front, which has the required number of ends required for the warp of the fabric.
|