Cotton drill is a medium weight, single cloth, weighing from 4 to 6 ounces and composed of coarse all-cotton yarns, warp and filling. It Is always made with a small uneven sided twill weave, generally (warp effect) twill weave. Drill is sometimes made from yarns in the gray and afterwards dyed In the piece, or in solid warp color effects, such as indigo blue and dark brown, white filling being used in each instance. It can be woven in any single box roller loom, and is usually drawn in and woven on cotton harness, as these are light in weight and wear better than wire heddles for this style of cotton goods. The lighter weights were used for Shirts, Safari jackets, martial art wear, cook's uniform.
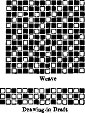
|
Carding and Spinning Particulars. The machinery used to make the counts of yarns for the kind of cloth under description would be found in mills of the first and perhaps of the second division, as given in a previous lesson. As the yarns are made from a short staple, low-grade cotton, the mixing will probably be done by hand; i. e., the bales of cotton would be opened at the mixing bin and the cotton separated into small parts and piled up in the bin until it was full. The good waste from cards and drawing frames would also be mdxed in with the raw stock, and in the cheaper grades of drill comber waste is sometimes used in small quantities. The same length of staple may be used for both warp and filling yarns and they may be run through the same machines up to the fly frames, and here THE ONLY DIFFERENCE is that the roving to make the filling yarn is run through one more process of fly frames than the warp yarn. The mixing isi taken from the bins and thrown into the hopper of the opener and this hopper is always kept full. Keep the pin beater free from cotton, so that an even sheet of cotton may be passed up to the beater, the speed of which should be about 1,050 revolutions per minute. In modern mills this opener is built in connection with the breaker picker, and the cotton, after 'passing the beater, is thrown on to a moving lattice and is brought to the feed rolls of the breaker picker, which in turn condenses it and passes the beater which should have a speed of 1,500 revolutions per minute. See that the draught of this picker and also the finisher picker is so directed that the cotton, after passing the beater, will be blown upon the top of the pair of cages, as this will |
THE WARP is beamed on the slasher, the warp proper being divided into a certain number of sections, in accordance with the number of ends to 'be used in the drill warp. These sections are beamed on the warp mill, the yarn being run on to the beam from the spools in the creel rack. The several section beams, when completed in the warp mill, are assembled in the beam rack at the end of the slasher and the yarn from each beam is run through the size tub and over the drying cylinder of the slasher at the same time, on to the slasher beam, thus making a complete warp, the sizing and beaming being done at one operation. Slasher warps do not have a lease in them, the yarn being kept nearly straight in place by the use of a slasher comb, which is, in fact, a shallow reed having one open side. The comb is pressed through the threads, while they are' spread taut in the slaslher frame and a wooden cap is then fastened upon the open side of the slasher comb, thereby holding the yarn in place for the operation of drawing in. The drawing in is performed by girls, without the aid of a hander in, as is the case when pattern warps are drawn in from a lease. The drawer in for drill, uses a three-bladed hook (a blade for each harness) and the harnesses or heddles are hung upon a rack immediately in front of the beamed wary. The drawer in, if experienced, will pick out three heddles and three ends at one time, and continue to do so until the total warp ends are threaded through the harnesses or heddles. To finish colored drill, the goods are taken from the loom and run through the brusher, to remove all lint and waste threads, after which they are put through the size tubs and then dry pressed.
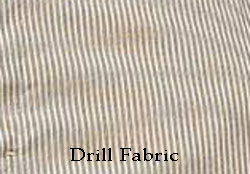
|
HELP TO MAKE AN EVEN LAP at the front end. The weight of the lap at the front end' of the breaker should be about 40 pounds or about 16 ounces to the yard. The laps are then put up at the finisher picker and doubled four into one. The speed of this beater should be 1,450 revolutions per minute and the weight of the finished lap about 39 pounds or 14 ounces to the yard. The cotton receives about 42 beats to the inch at this machine. The draft of this machine is very small and very rarely exceeds 3. All heavy and quickly moving parts should be oiled frequently and keep the room clean. The laps are then put up at the card. The draft of this machine should not exceed 100 for this class of goods.
THE SETTINGS should be v»ide, because it is the object to get off as many pounds as possible for this class of goods. Keep the wire sharp by frequent grindings. The speed of the licker-in should be about 300 revolutions per minute. The speed of the top flats should be one complete revolution in 40 minutes and tho speed of the doffer from 13% to 14 revolutions per minute. The diameter of the doffer should be as large as possible, say 26 or 27 inches. The production should be about 800 pounds for a week of 60 hours.
THE SLIVER should weigh about 65 grains to the yard. The sliver is run through three processes of drawings, the weight at the finisher drawing being 70 grains. The doublings at the different processes of drawing should be 6 into 1 and the drafts should not exceed 6. The speed of the front roller should bo 400 revolutions per minute. The slubber is the next process, and here the sliver should be made into a 50 hank roving. The warp yarn is then put through one more process of fly frame and made into 1.25 to 1.50 hank roving and from here passed to the spinning room. The filling yarn is put through one more process and is made into 2.50 hank roving and then passed on to the spinning room.
THE SPINNING FRAME then draws the roving into the required hank by having the correct draft gear put on. Good specifications for both the warp and filling frames are as follows: for warp frame, for spinning 10s yarn, gauge of spindle. three inches: diameter of ring, two Inches; length of traverse, 7 inches; speed of spindle 8,600 revolutions per minute; twist per inch, 15.02; for filling frame spinning 18s yarn, gauge of spin-die, 2% inches; diameter of ring, 1% inches; speed of spindle, 7,200 revolutions per minute; length of traverse, 6% indies; twist per inch, 13.79. The warp yarn is then spooled, warped and run through a slasher |